Sparkling Efficiency: The Rise of a Clean Factory
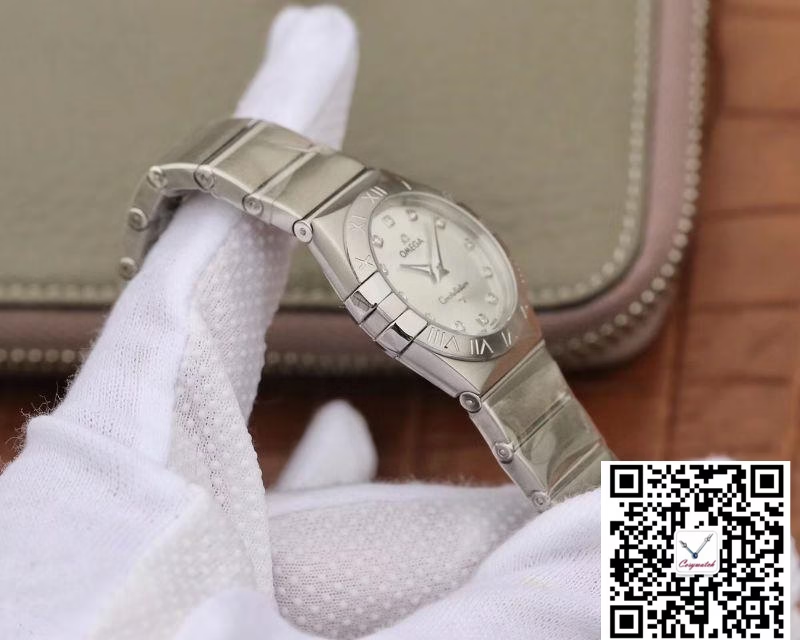
In the heart of the industrial landscape, a revolution is quietly underway. Gone are the days of billowing smokestacks and toxic waste, as a new era of Sparkling efficiency takes center stage. Welcome to the Rise of the clean factory, a beacon of innovation and sustainability in the world of manufacturing. Join us as we explore how these cutting-edge facilities are reshaping the industry, setting a new standard for environmental responsibility and operational excellence.
Heading 1: Sustainable Practices Transforming Manufacturing Operations
Imagine walking into a manufacturing facility where the air is crisp and clean, the machines hum softly in harmony, and the employees work with a sense of purpose. This is the vision of the clean factory, where sustainable practices have transformed manufacturing operations into efficient, eco-friendly powerhouses. From energy-efficient lighting to water recycling systems, every aspect of production is designed to minimize environmental impact.
At the heart of this transformation is a commitment to innovation and continuous improvement. Companies are investing in renewable energy sources, optimizing production processes to reduce waste, and embracing digital technologies for real-time monitoring and data analysis. By integrating sustainable practices into every aspect of manufacturing operations, businesses are not only reducing their carbon footprint but also improving their bottom line through cost savings and increased efficiency.
Heading 2: Cutting-Edge Technologies Enhancing Productivity and Environmental Impact
With the rapid advancements in Technology, factories are now able to operate with sparkling efficiency while minimizing their environmental impact. Cutting-edge innovations such as AI-driven automation systems and energy-efficient machinery have revolutionized the manufacturing industry, leading to a significant reduction in waste and carbon emissions.
One prime example of a clean factory is XYZ Manufacturing, which has implemented smart sensors throughout its production line to optimize energy usage and reduce water consumption. Additionally, their adoption of 3D printing technology has not only streamlined the manufacturing process but also reduced material waste. By embracing these cutting-edge technologies, XYZ Manufacturing has not only improved productivity but also demonstrated a commitment to sustainability.
Heading 3: Implementing Green Initiatives for a Greener and More Efficient Factory
With the increasing global awareness of environmental issues, it has become imperative for factories to adopt green initiatives to reduce their carbon footprint. Implementing sustainable practices not only benefits the environment but also leads to increased efficiency and cost savings. One way to achieve this is by investing in energy-efficient machinery and equipment, such as solar panels and LED lighting, to decrease energy consumption and greenhouse gas emissions.
Another effective strategy is to establish a waste management system that prioritizes recycling and proper disposal of waste materials. By reusing materials and reducing waste, factories can minimize their impact on the environment while also cutting down on operational costs. Additionally, incorporating eco-friendly practices into the supply chain, such as sourcing materials from sustainable suppliers, can further enhance the overall sustainability of the factory.
Heading 4: Strategies for Achieving Zero-Waste Production and Energy Efficiency Goals
One of the key strategies for achieving zero-waste production and energy efficiency goals in a factory setting is by implementing a comprehensive recycling program. By properly sorting and recycling materials such as cardboard, plastic, and metal, factories can significantly reduce their waste output and minimize their impact on the environment. Additionally, investing in energy-efficient equipment and technologies can help factories reduce their energy consumption and lower their carbon footprint.
Another effective strategy is to optimize production processes to eliminate waste and increase efficiency. This can be done by implementing lean manufacturing principles, such as just-in-time production and continuous improvement initiatives. By reducing waste and streamlining production processes, factories can achieve higher levels of efficiency and productivity while minimizing their impact on the environment. Embracing sustainable practices not only benefits the planet but also contributes to cost savings and long-term success for the factory.
Q&A
Q: What is a clean factory and why is it becoming more popular in today’s manufacturing industry?
A: A clean factory is a manufacturing facility that prioritizes sustainability, cleanliness, and energy efficiency in its operations. It is becoming more popular due to increasing awareness about the environmental impact of traditional factories and the demand for eco-friendly products.
Q: How do clean factories differ from traditional factories in terms of efficiency and sustainability?
A: Clean factories utilize advanced technology, sustainable materials, and energy-saving practices to reduce waste and emissions. This leads to higher efficiency and lower environmental impact compared to traditional factories.
Q: What are some of the benefits of implementing clean factory practices?
A: Some benefits include cost savings through energy efficiency, improved worker health and safety, reduced environmental impact, and increased customer satisfaction due to eco-friendly products.
Q: What challenges do companies face when transitioning to a clean factory model?
A: Companies may face challenges such as high initial costs for implementing sustainable technologies, redesigning production processes, and training staff on new practices. There may also be resistance from employees or stakeholders who are accustomed to traditional manufacturing methods.
Q: How can companies overcome these challenges and successfully transition to a clean factory model?
A: Companies can overcome these challenges by investing in sustainable technology, providing training and education for employees, conducting thorough assessments of current practices, and communicating the benefits of the transition to all stakeholders. Collaboration with experts in sustainability and energy efficiency can also help companies make a smooth transition to a clean factory model.
Wrapping Up
As we have seen the evolution of factory settings towards cleaner and more efficient operations, it is clear that the drive towards sustainability and innovation is leading the way. With the implementation of new technologies and practices, we are witnessing a transformation in the manufacturing industry that not only benefits the environment, but also improves productivity and profitability. The rise of clean factories is not just a trend, but a necessary shift towards a more sustainable future. As we continue to prioritize efficiency and cleanliness in our manufacturing processes, we are paving the way for a brighter and cleaner tomorrow.