Spotless Operations: The Journey to a Clean Factory
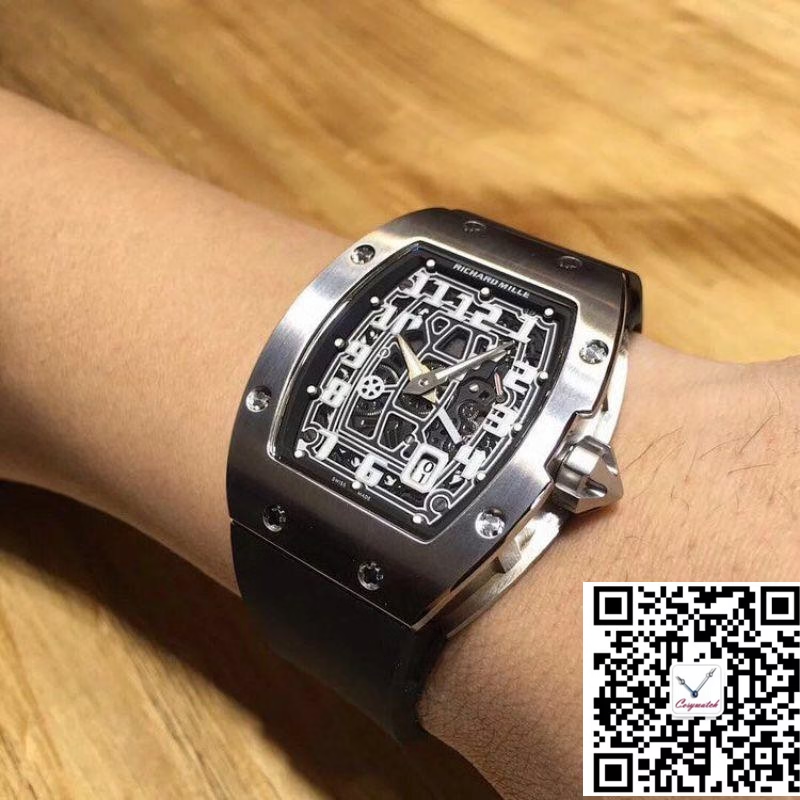
In the world of manufacturing, cleanliness is not just a matter of aesthetics - it’s a crucial element for ensuring smooth operations and product quality. As we delve into the world of Spotless operations, we uncover the journey that factories take to achieve pristine conditions. Join us on this exploration of the meticulous processes, innovative technologies, and dedicated teams that make a factory truly clean and efficient.
The Importance of Maintaining a clean factory Environment
Having a clean factory environment is essential for the smooth and efficient operation of any manufacturing facility. A spotless factory not only improves the overall aesthetics of the workplace but also plays a crucial role in ensuring the safety and well-being of employees. Here are a few reasons why maintaining a clean factory environment is of utmost importance:
- Enhanced Productivity: A clean and organized factory floor allows employees to work more efficiently, reducing the time spent searching for tools and materials.
- Improved Safety: A clutter-free environment minimizes the risk of accidents and injuries, creating a safer workplace for everyone.
- Regulatory Compliance: Many industries have strict cleanliness standards that must be met in order to comply with regulations and avoid costly fines.
By prioritizing cleanliness and maintenance in your factory, you not only create a more pleasant working environment but also contribute to the overall success of your operations. Investing time and resources into keeping your factory clean will pay off in the long run, resulting in higher productivity, improved employee morale, and better compliance with industry regulations.
Strategies for Implementing Effective Cleaning Protocols
When it comes to maintaining a clean factory, implementing effective cleaning protocols is essential for ensuring spotless operations. One strategy is to establish a regular cleaning schedule to keep all areas of the factory clean and organized. This includes daily, weekly, and monthly tasks to address different levels of cleaning needs.
Another key strategy is to train all employees on proper cleaning techniques and procedures. Providing training on the use of cleaning products, equipment, and safety protocols can help ensure that all staff members are equipped to maintain a clean and safe working environment. Additionally, creating a culture of cleanliness and accountability among employees can help promote a shared responsibility for keeping the factory clean and well-maintained.
Technological Advancements in Factory Cleaning Equipment
In the fast-paced world of manufacturing, cleanliness and hygiene are essential for ensuring smooth operations. Thanks to , maintaining a spotless environment has never been easier. From automated floor scrubbers to high-pressure washers, these innovative tools are revolutionizing the way factories maintain cleanliness.
One such advancement is the introduction of robotic cleaning machines, which are capable of navigating through tight spaces and efficiently cleaning hard-to-reach areas. These robots are equipped with sensors that allow them to detect and avoid obstacles, making them a safe and effective solution for keeping factories clean. Additionally, the use of water-saving technologies in pressure washers helps to conserve resources while still achieving optimal cleanliness. With these cutting-edge tools at their disposal, factory managers can ensure that their operations run smoothly and efficiently.
Best Practices for Sustaining Spotless Operations
When it comes to maintaining spotless operations in a factory setting, there are several best practices that can help ensure a clean and organized work environment. One key practice is to implement regular cleaning schedules for all areas of the factory, including production floors, break rooms, and bathrooms. This can help prevent the build-up of dirt, dust, and other contaminants that could compromise the quality of products being manufactured.
Another important practice is to designate specific cleaning tasks to employees or teams, ensuring that everyone takes ownership of keeping the factory clean. Providing adequate training on proper cleaning techniques and the safe use of cleaning supplies can also help maintain spotless operations. Additionally, investing in high-quality cleaning equipment and supplies, such as industrial-strength vacuums and disinfectants, can help ensure that the factory remains clean and sanitary at all times.
Q&A
Q: What is the importance of maintaining a clean factory?
A: Maintaining a clean factory is crucial for ensuring the safety of employees, compliance with regulations, and optimizing operational efficiency.
Q: What are some common challenges faced in keeping a factory spotless?
A: Some common challenges include managing waste disposal, implementing effective cleaning protocols, and maintaining cleanliness in hard-to-reach areas.
Q: How can employees contribute to maintaining a clean factory?
A: Employees can contribute by following proper cleaning procedures, reporting any spills or hazards promptly, and practicing good housekeeping habits.
Q: What are the benefits of having a clean factory?
A: Benefits of having a clean factory include improved employee morale, reduced risk of accidents, increased productivity, and enhanced reputation with customers and regulators.
Q: What role does management play in achieving a spotless operation?
A: Management plays a crucial role in setting and enforcing cleanliness standards, providing the necessary resources and training, and fostering a culture of cleanliness throughout the organization.
Concluding Remarks
In conclusion, maintaining a spotless factory is not just about cleanliness; it’s a journey towards efficiency, safety, and sustainability. By implementing the right practices and continuously monitoring and improving operations, companies can create a clean and organized workspace that not only boosts productivity but also enhances the overall working environment for employees. So, let’s embark on this journey to a clean factory together, and reap the benefits of spotless operations.